ものづくりの流れFlow
はじめに
ステップを適切に仕分けるけることで、手戻りのによる時間の短縮やコストダウンにつながっていきます。 ここでは、「ものづくり」を5ステップに分けて、製品の制作過程を紹介します。業界や企業によって、違いがあることもありますが、初めての方や、生産までが順調にすすまない方などは参考にしてください。 |
製造の流れ
ここで紹介する制作過程は五つ。各ステップ(工程)を紹介します。
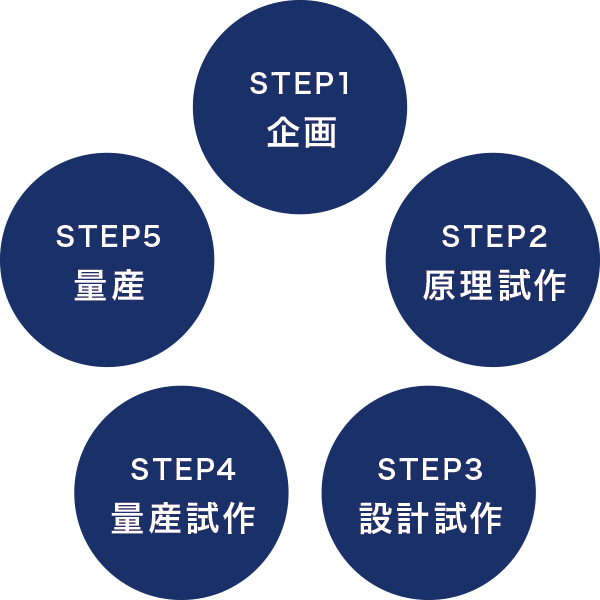
次から、各ステップの概要やチェックポイントを紹介していきます。
また、それぞれの段階で確認を行うデザインレビュー(設計審査)が製品量産に向け重要な役割を果たします。
また、それぞれの段階で確認を行うデザインレビュー(設計審査)が製品量産に向け重要な役割を果たします。
- STEP1
- 企画
新商品の開発には、大別してユーザー要望を重視したマーケットインタイプやメーカ側から新技術や付加価値を提供するプロダクトアウトタイプがあります。 マーケットインの代表例では、ユーザの具体的な課題解決を目的とした商品があげられます。 イメージしやすい仮想製品を考えると、「要求:工事現場で安心して使えるスマートフォンが欲しい。提供:防塵防水で落としても壊れにくいスマートフォンを販売」などが考えられます。 プロダクトアウトの代表例では、メーカの技術力により市場に新しいサービスや製品を提供する事があげられます。 マーケットインの事例に関連すると、スマートフォン自体が今までに無かった製品を提供した事例となります。 |
近年では、上記2つのどちらかではなくどちらの要素も取り込んだ開発が主流になりつつあります。
ターゲット(客層)の選定、製品のセールスポイント、開発要求の順位付けなどがあります。
並行して、市場や類似製品などの調査も行います。
このステップで重要かつ見落としがちな項目が、開発要求の順位付けとなります。
すべての要求を満たすことは、まずありません。
多機能でありながら、小型で耐久性が高く、そして安価に。スペック(機能の要求)と量産コストが釣り合わないなど、実際によくある事例です。
企画は製品開発の基礎となるステップですので、一番おざなりにはできない工程です。
ターゲット(客層)の選定、製品のセールスポイント、開発要求の順位付けなどがあります。
並行して、市場や類似製品などの調査も行います。
このステップで重要かつ見落としがちな項目が、開発要求の順位付けとなります。
すべての要求を満たすことは、まずありません。
多機能でありながら、小型で耐久性が高く、そして安価に。スペック(機能の要求)と量産コストが釣り合わないなど、実際によくある事例です。
企画は製品開発の基礎となるステップですので、一番おざなりにはできない工程です。
- STEP2
- 原理試作
他の試作と異なる点として、機能の実現に重点をおきます。最近はPoCと呼ばれる事もあります。 この試作段階で、詳細設計を行うと、再設計・試作に時間とコストが発生してしまいます。そこで、既存の製品などを利用することによって、モジュール単位での交換で済みますので、短期で検証が行えます。 例をあげれば、 ・製品の液晶画面の代わりに、PCのアプリケーションに表示させる ・モータ制御ユニットを既存のキットを使う このステップでは、簡単に修正ができる手法を用いて、製品の機能を確認していきます。先にも書きましたが、本番で使用する金型などを作成すると、設計変更時に大幅な時間やコストが発生します。 |
関係者が実物をみて、認識を統一させる目的も含まれています。
筐体の外形は3Dプリンターで作る事で、さまざまな外形でテストを行うことが容易となりました。
電子回路設計では、Arduinoを代表とする開発ボードなどや各種機能モジュールを組み合わせることで開発が容易になりました。
原理試作で作ったサンプルで、実際のユーザーに見てもらい評価や意見を聞くことや
展示会などで発表を行うこともあります。
筐体の外形は3Dプリンターで作る事で、さまざまな外形でテストを行うことが容易となりました。
電子回路設計では、Arduinoを代表とする開発ボードなどや各種機能モジュールを組み合わせることで開発が容易になりました。
原理試作で作ったサンプルで、実際のユーザーに見てもらい評価や意見を聞くことや
展示会などで発表を行うこともあります。
- STEP3
- 設計試作
実物を制作することで、サイズや機能が十分に備わっているか、生産費用の算出などを行います。 ここで作られた製品は、テスト用に使われたりします。環境(温度・湿度等)や耐久テストなどを経て、次のステップへの進みます。 この段階で、企画段階で求められている要求を満たしている物が形となります。 量産を視野にいれた設計を行うため、部品調達に関する検討や組立先の選定など、設計者だけでなく量産工程の意見も取り入れつつ行うことが重要となります。 |
- STEP4
- 量産試作
実際の組み立て現場(工場)で作成してもらいます。作業員の技量による組み立て難易度、製造時間や、実際の仕入れ先からの部品を利用して不良率の確認などを行います。 このステップの目的は、一回で大量(ロット)に作ることで、統計的に製品の品質や生産コストを知ることです。 STEP3「設計試作」と同様、テストを行います。開発者が制作した製品と、作業員が製造した製品とでは求められる品質が異なるので、このステップでのテストが一番重要だといえます。 メーカによっては量産試作品は、実際に販売する商品として使用するケースもあります。試供サンプルや店頭サンプルとして配布で使用し、実際に販売するのは受注後の量産からといったケースもあり、ここは各メーカの考え方次第となります。 |
- STEP5
- 量産
■デザインレビュー(設計審査) 各工程で、それぞれの部門の担当者がレビュー(評価)を行います。 それぞれの部門の視点から、各試作やテスト結果などを評価していきます。 各工程で評価を行うことで、問題点など洗い出すことで、量産までのトラブルを回避していくことが目的となります。 |
おわりに
ものづくりを成功に導くステップの一例を紹介してきました。
ソフトウェアやサービスなどにも共通しますが、プロジェクトは、工程の区切りを明確にし、また複数人の視点から評価をすることが成功への近道となります。
「何から手を付ければよいのか?」「順調にいかない理由は?」などの疑問に対して、ヒントになれば幸いです。弊社では「ものづくり」のサポートを行っておりますので、お気軽にご相談ください。
ソフトウェアやサービスなどにも共通しますが、プロジェクトは、工程の区切りを明確にし、また複数人の視点から評価をすることが成功への近道となります。
「何から手を付ければよいのか?」「順調にいかない理由は?」などの疑問に対して、ヒントになれば幸いです。弊社では「ものづくり」のサポートを行っておりますので、お気軽にご相談ください。